Turbochargers and superchargers | Difference
Turbocharged or supercharged engines with reduced displacement are attracting increased consideration as a means of achieving better part-load fuel economy in automobiles.
Naturally aspirated
When at atmospheric pressure , engine takes fresh charge into the cylinder and after burning exhausts directly into the atmosphere is called naturally aspirated engine.
Supercharged engine
Before putting air or charge into the cylinder, it is possible to add a crankshaft-driven compressor to increase the pressure of the air (or mixture). This leads to more mixture to be burnt in a given volume of cylinder. The unit driven by the crankshaft is called supercharger (although this is sometime termed as turbocharger as well)
Turbocharged engine
Exhaust leaving from engine contains significant amount of energy which has not been used by engine and therefore can be used to drive the compressor. Engine having such configuration is called turbocharged engine.
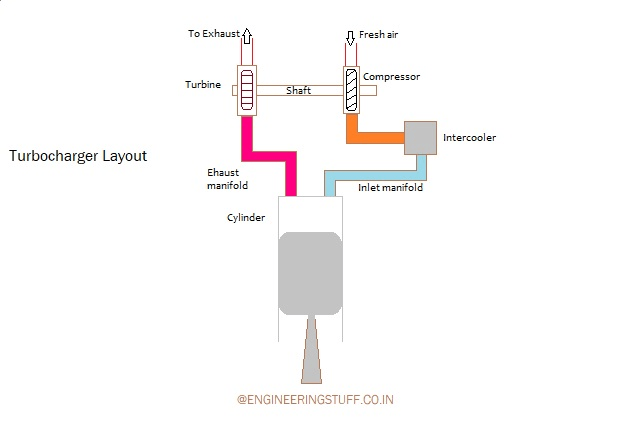
It is obvious to have temperature increased after the compression and to tackle this a air cooler is placed which is called intercooler which also helps increase density of air by reducing temperature. Intercooler are used with both turbochargers and superchargers.
Most supercharged or turbocharged production applications use a single unit, in many cases followed by a charge air cooler. With some cylinder configurations, two smaller turbochargers may be used instead of one larger unit. The primary reason for such a layout is improved packaging. The smaller turbochargers also reduce acceleration lag, but result in an efficiency penalty due to higher fluid friction losses with the smaller passage sizes.
A single unit is used in most supercharged or turbocharged applications, often accompanied by a charging air cooler. In certain cylinder setups, instead of one larger unit, two smaller turbochargers can be used. Improved packaging is the main benefit of such setup. The smaller turbochargers improves acceleration but with the smaller passage volumes efficiency gets reduced due to higher fluid friction losses.
As the need for higher specific performance increases, more complex configurations are going into development, both for improved part-load productivity and for decreased package volume and weight. A turbocharger has long been used on two-stroke diesel engines in series with a supercharger, formerly in heavy truck applications, and still used today in some marine engines. Under all operating conditions, the two-stroke needs pressurized intake air, and The crankshaft-driven supercharger fulfills this need. Turbocharger in series with the supercharger helps the individual output to be improved and by using more of the exhaust energy, increases engine performance. This configuration is often used on four-stroke car engines as well.
With intake air drawn first from a low pressure compressor and then a high-pressure compressor, two turbochargers can be mounted in succession. An intercooler can be positioned between two turbochargers followed by the aftercooler placed after second turbochargers. First the exhaust gas travels through the high-pressure turbine, and later through the low-pressure turbine. In the series configuration, under all operating conditions, the intake charge and exhaust gas flow into both units. In heavy truck engines, this configuration is often used, and is Popular in diesel engines that are bigger, off-highway.
Sequential turbocharging is referred to as a more modern configuration. This design uses both low- and high-pressure turbochargers and with intake and exhaust control valves flow is directed through either the high-pressure or low-pressure turbocharger and through both turbochargers partially under only certain conditions. This design facilitates the conservation of high specific performance over a large range of engine speeds. Production applications for series and sequential turbocharging systems are currently being introduced in diesel engines, where the extra boost pressure can be more readily used to increase individual performance. Sequential turbocharging is now being used with careful monitoring and machine optimization in a few output spark-ignition applications. Within knock limits, the combustion system must be tuned, but the sequential turbochargers allow a wide speed range at high specific output.
Recent Comments