What is Polarity in Arc welding
For an arc process to work, the electrical polarity that is given to the arc via the power source is crucial. The major polarity impacts on welding are determined by the direction of current flow in the arc. Since it is usual to see current described in welding literature as flowing in the direction of electron flow, from the negative to the positive electrode, there is a chance that the direction of current flow will be unclear. However, current is typically defined as moving in the direction of positively charged ions or from the positive electrode to the negative electrode.
Electrons travel from the negative electrode (cathode) to the positive electrode (anode) for a welding arc in any circumstance, although this has varied impacts with different procedures. When the work is positive and the electrode is negative, this is known as arc welding’s DCEN (DC electrode negative) or, more formally, DCSP (DC straight polarity). The welding electrode releases electrons into the arc, where they go to the work. It is known as DCEP (DC electrode positive) or, more formally, DCRP (DC reverse polarity) when the electrode is positive in relation to the work. Other polarity choices include VP (variable polarity), which refers to voltage wave patterns that are more complicated and changeable than basic AC, and AC (simple alternating current).
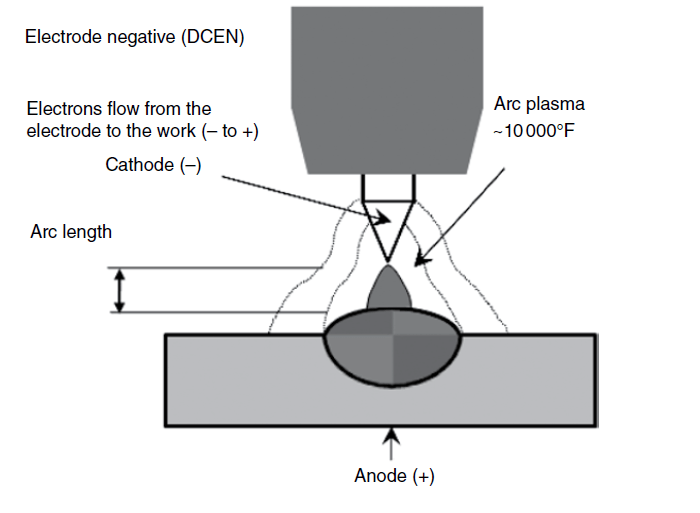
The polarity and direction of electron flow change in both scenarios. The procedure and the properties of the material being weld affect how polarity affects heat input and arc behavior. The most frequent polarity for GTAW is DCEN, which generates the majority of the heat into the work. The tungsten electrode can be heated to extremely high temperatures without melting, which explains this. Thermionic emission is a technique that makes it simple for electrons to be released or “boiled off” from the tungsten electrode (cathode) at the extremely high temperatures. With the majority of the arc heat deposition occurring at the work piece where the electrons are deposited, this results in a stable arc.
The tungsten arc is irregular while working with DCEP polarity because electron emission is challenging at the lower work temperature. However, DCEP can be advantageous when welding aluminum because the electron emission process, also known as cleaning action, can assist remove the stubborn aluminum oxide from the surface. The fact that AC current gives both a half-cycle of DCEN, which warms the work piece, and a half-cycle of DCEP, which eliminates the oxide, makes it useful in this situation. Due to the lower melting temperature of the bare electrode wire during GMAW, thermionic emission is not possible using DCEN. As a result, DCEN generates an arc that is very unpredictable and challenging to manage.
With DCEP, the work is negative and the area where the electrons may be released most steadily receives the most heat. This is mainly because the work surface’s oxides make the electron emission process easier. Because of how much more stable the arc becomes as a consequence, GMAW nearly always employs DCEP polarity. Depending on the kind of flux and the application, processes using fluxes like SMAW, FCAW, and SAW can employ DCEP, DCEN, or AC polarities. When the electrode is the cathode (DCEN), flux enhancements that come into contact with the welding electrode might encourage electron emission.
This makes the DCEN polarity a sensible process option. In certain circumstances, DCEN may be chosen to generate higher deposition rates through increased electrode heating with lower heat input to the task. Additionally, it may be utilized to weld thinner materials.
Recent Comments