Fuel system of Diesel engine explained in detail
The original patent application by Otto Diesel for what we now know as a diesel engine was pretty vague about the type of fuel it could use: he also suggested the possibility of coal dust. Many boat owners seem almost as vague: in boats that literally run out of fuel, lifeboats have to tow every year!
Nonetheless, there’s more to bring gas into an engine than just dump it into the tank. Diesel fuel does not burn very easily, and it has to be in the form of fine droplets, like an aerosol spray, to burn quickly, cleanly and reliably. You must note that the air in the cylinders of a diesel is made warm by being heated to 20 to 30 times the normal atmospheric pressure, so creating an aerosol spray inside the cylinders means that the gas must be at an even higher pressure – in the order of 2,500 psi.
It is also important to accurately measure the ratios of fuel and air, so each spray of fuel must be calculated very accurately. If you think of a typical four-cylinder diesel that develops 80 hp when it runs flat at 4,000 rpm, about 4 gallons of fuel per hour will be burned.
Each cylinder will be receiving 2,000 sprays of fuel every minute – making 8,000 sprays per minute, or 480,000 sprays per hour.Therefore, that spray must be less than a gallon of 10 millionths, 0.04 ml, or less than a hundredth of a tablespoon.The amount of fuel sent to the cylinders must be even smaller at low loads.
It is hardly shocking, then, that the fuel system contains some of the engine’s most complex and costly components, responsible for achieving nearly 200 atmospheric pressures, calculating precise fuel doses to less than a thousandth of a milliliter, and repeating the process maybe half a million times an hour!
The basic fuel system of diesel engine:
The fuel system starts, however, with the crudest component of all: the tank. However, it is worth keeping in mind that a full tank can be very large, so against the movement of the vessel it needs to be well protected and secured. A big tank – anything over around 5–10 gallons – should include internal baffles to avoid the fuel from moving around, and any tank requires a vent, or ‘ breather, ‘ to let air in as the fuel is consumed.
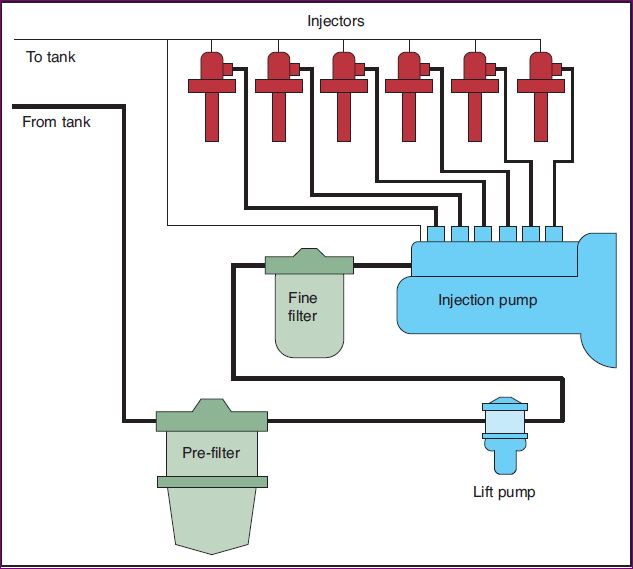
The fuel obtained from the pipe may not be perfectly clean, and the air entering through the breather will almost certainly be sufficiently moist to cause condensation to develop within the tank. The final result is that some soil and water will be included in the tank.
To stop this affecting the engine, an element known as a primary filter, pre-filter, separator, sedimenter or filter-agglomerator, normally installed on a bulkhead in the engine compartment rather than on the engine itself, should be included in the engine installation.
It is the responsibility of the lift pump to take the fuel out of the tank, through the primary filter, and move it to the rest of the system.It is a basic diaphragm pump in most situations, much like a miniature version of a manual bilge pump.The motor powers it, but normally has a hand-operated priming lever to pump fuel through the process without running the engine.
The fuel then passes through another filter, also known as the main filter or secondary filter or fine filter, whose task is to eliminate dirt particles that may be too small to see at less than a thousandth of a millimetre, but can still wear the very finely built surfaces of the rest of the system.
If a diesel engine has a heart, it must be the injection pump, because the fuel is measured and pressurized there. Injector pipes, with very thick walls to withstand the pressure, carry the highly pressurised fuel from the injection pumps to the injectors that spray it into the cylinders.
However, some of the fuel pumped into the injectors never actually reaches the cylinder, but is returned to the tank via a leak-off pipe or return line.
Recent Comments