What is Arc voltage in welding
Working arc voltages generally vary from 10 to 40 V. Arc voltage and arc lengths are largely connected. Higher arc voltages are produced by longer arc lengths, whereas lower voltages are produced by shorter arcs. The voltage (potential) variation through the arc is seen in Figure. The voltage distribution or drop over the arc is mostly found around the anode and cathode, as seen in the image. In the figure, the work piece serves as the positive electrode’s anode drop or fall, and the welding electrode serves as the negative electrode’s cathode drop or fall.
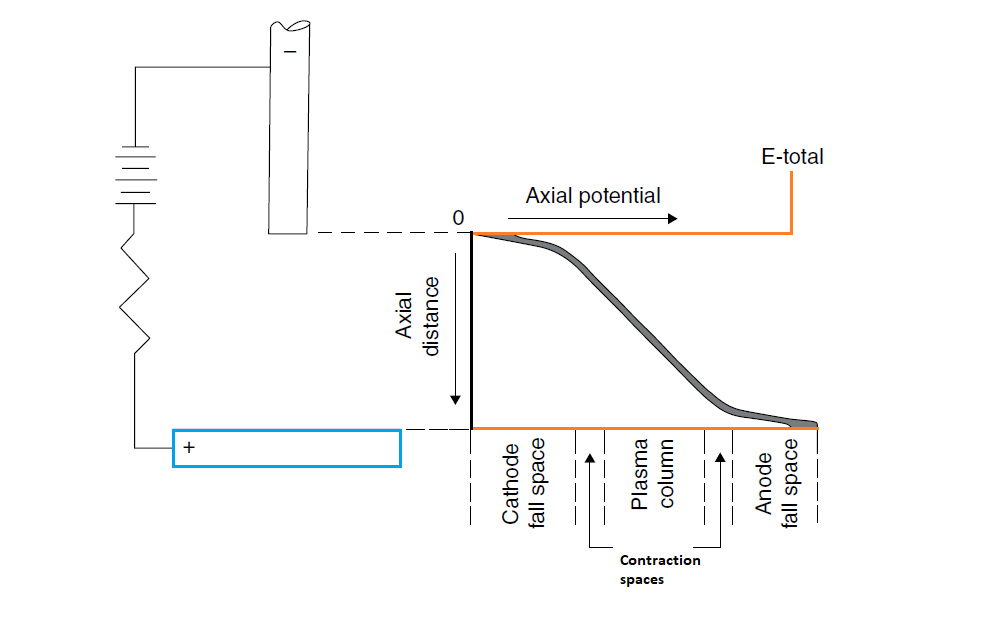
The plasma column, which is the area between the anode and cathode drops, is known to be responsible for the majority of the change in arc voltage as a function of arc length. The arc length is known to have a negligible impact on the anode and cathode drops. As a result, voltages significantly larger than zero can be seen in even very small arc lengths. This shows that the two voltage dips at the electrodes are where the majority of the arc voltage is located.
These voltages may account for as much as 80–90% of the overall arc voltage for a typical welding arc length. The quantity of power dissipation must thus be highest at the electrode drop areas and not in the plasma column since power dissipation and heat generation are factors of voltage and current and the level of current is uniform throughout the arc. Due to their extraordinary narrowness, these anode and cathode drop zones’ effects are not visible on arc thermal diagrams. The arc temperature alone does not fully explain why the arc is a useful heat source for welding, but they also play a crucial part in the melting at the anode and cathode.
To ionize a gas over a given gap and gas pressure, higher voltages are necessary. For a welding arc, the latter is typically atmospheric pressure; however, arc welding may also be done under different pressure circumstances, such as underwater or in a chamber. It is not sufficient to merely break down a gap since the open circuit voltage typical of power supply (60-80 V) is rather low. The electrode must typically be touched, so-called scratched, or dragged on the work piece when using manual arc welding procedures. It is known as “triking” or “rawing” an arc when this happens because it results in an immediate short circuit current from the power source.
The gap can be widened to produce a steady arc after the ionization process has begun. In semi-automatic procedures, the wire feed mechanism drives the wire into the work piece, causing a short circuit. Response to that, the power source generates an extremely high short circuit current that quickly burns the wire creating the gap. In order for the welder to start the arc without contacting the tungsten electrode to the workpiece, specific arc starting systems for GTAW are included into the machine. These systems apply high voltage at a high frequency. The performance of the tungsten electrode might be impacted by pollution in the weld or on the electrode tip.
Recent Comments