3d Printer | How 3d printing is done
3D printing is process of creating 3- dimensional solid object from a computer aided design file and robots.
3d Printing is based upon the principle of additive manufacturing so this is also called as additive printing. In the additive manufacturing process a 3d object is created by placing successive layers of material one upon another until the object is complete.
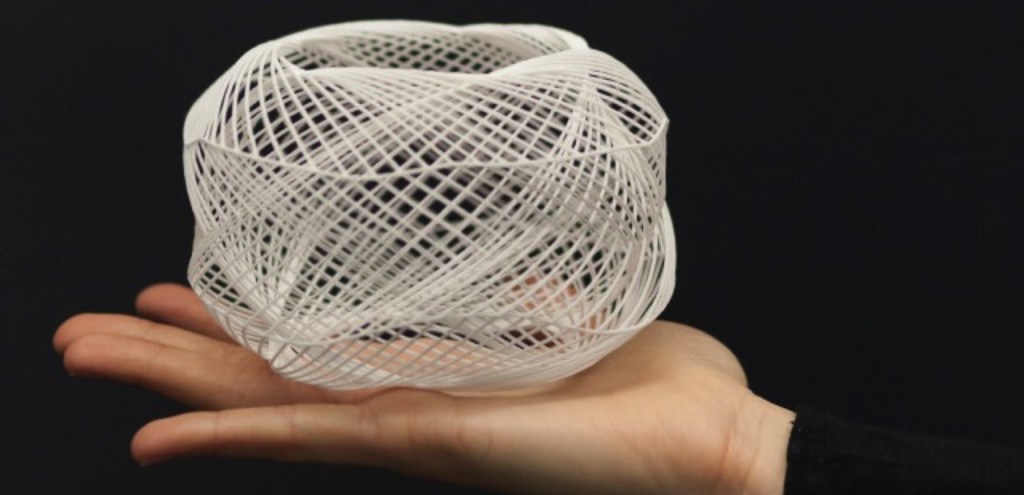
As mentioned above it is computer aided process so the design of product to be manufactured is made as 3d model. Then the path or the route which the robotic arm will follow , the speed of the arm and parameters required to automation of robot is given to the control unit of robot.
The layers formed can be seen as a thinly sliced horizontal cross-section of the eventual object. As in subtractive manufacturing or general manufacturing where we cut a object or shape a object by removing successive layers of material 3D printing is the opposite of subtractive manufacturing .
3D printing enables us to make very complex and complicated objects. The time it takes to manufacture is very less and the quality and precision is very high.
How 3D printing is done?
There are 3 main steps in 3D printing:
The First step is the designing and modeling of the object. this preparation is carried out before printing. 3D designs are made using design softwares like AutoCAD. Designing can be done in two ways, One is if object is already available or if prototype is available then the model can be made using scanned and reverse engineered and secondly if new object is to be created then the only way is to design step by step and make model.
When the model and design is ready we need to move to second step.
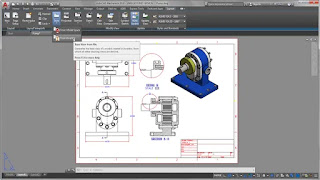
Second step involves the selection of material to be used ,3D printing involves variety of materials it includes glass, resins, plastics, biomaterials and many more.
It also includes selection of the robot and arm length according to the shape and size of object, The 3d manufacturing uses the robots for the precise work and if object is very large and the precision in not much required then this is done by manual moving arm which is handled by skilled operator.
In case of the robots , routing or selection of path of the robotic arm , Selection of the thickness of the feed or diameter of eject nozzle , Selection of speed of the arm which depends upon the drying speed of the material is done in this phase only.
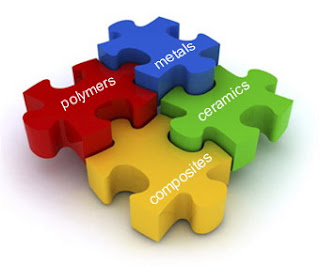
Third step is the inspection , aesthetic and finishing process. After completion if the 3D printing this step comes into play. In this step skills and tools are required as the printed object can not be used or delivered as it is, It has to be checked ,finished and polished. Variations in the thickness of wall is major problem, this is due to change in feeding rate and arm speed variations.
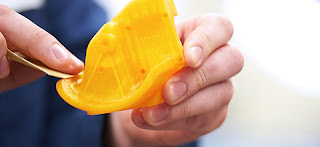
Learn more about 3D printing Here
Recent Comments