What is hooke’s law and stress strain curve?
Before knowing about Hooke’s law or stress strain curve one should know about stress and strain. Stress is, force applied on object per unit cross section area while strain is the ratio of change in dimensions of object to the original dimension.
Hooke’s law states that for small deformations, stress applied is directly proportional to strain.
Stress ∝ Strain
Or, Stress = E . Strain
E = Stress / Strain
where E is the modulus of elasticity or Young’s modulus of elasticity. The modulus of elasticity can be measured from the slope of the stress strain curve in the elastic region. The modulus of elasticity is related to the bonding strength between the atoms in a metal or alloy. Metals with high elastic moduli are relatively stiff. Inverse of the Young’s modulus of elasticity is known as compliance of the material.
Now let us understand Hooke’s law and each component of stress strain curve shown below:
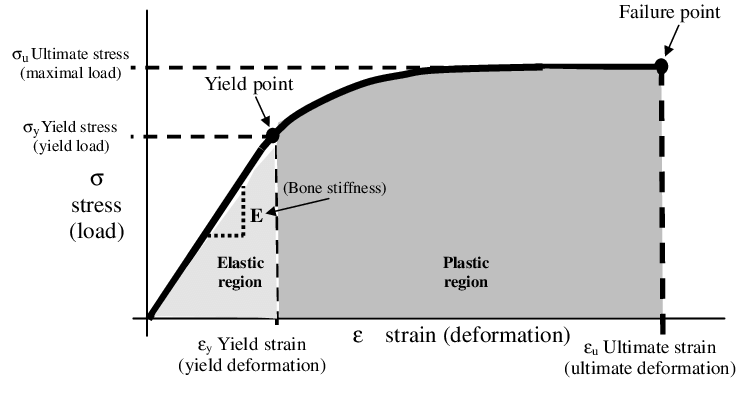
Elastic region: In stress strain curve whenever force is applied on any material initially it is deformed elastically. That is if the load is released from the part, it will return to its original shape and size. this property of materials is called elasticity and is drown on Stress strain curve as elastic region.
Yield point: According to hooke’s law , material initially exhibits elastic deformation however if we continue to increase the applied stress, the material begins to exhibit both elastic and plastic deformation. The material eventually ‘Yields’ to the applied stress. The critical stress value needed to initiate plastic deformation is defined as the elastic limit of materials. In metallic materials this is usually the stress required for dislocation motion or slip to initiate. The proportional limit is defined as the limit of stress above which the relationship between stress and strain is not linear. In most materials, the elastic limit and proportion limit are quite close. However, neither of them can be determined precisely.
Ultimate strength: Hooke’s law and stress strain curve also shows the ultimate strength which is the maximum strength reached in the engineering stress strain curve. If the specimen develops a localized decrease in cross section area , the engineering stress will decrease with further strain until the fracture occurs. The more ductile a metal is , the more the specimen will neck before fracture and hence more the decrease in the stress on the stress strain curves beyond the maximum stress.
Fracture point: Fracture point is the end point of the stress strain curve. When load is applied on the specimen, a stress will arrive where necking of the specimen starts and which further leads to fracture of specimen in to two pieces or more. The point on the stress strain curve where fracture of specimen occurs that point is called Fracture point.
Recent Comments